Efficiency In Motion: Streamlining Supply Chain For Electric Two-wheeler Sub-assembly Parts
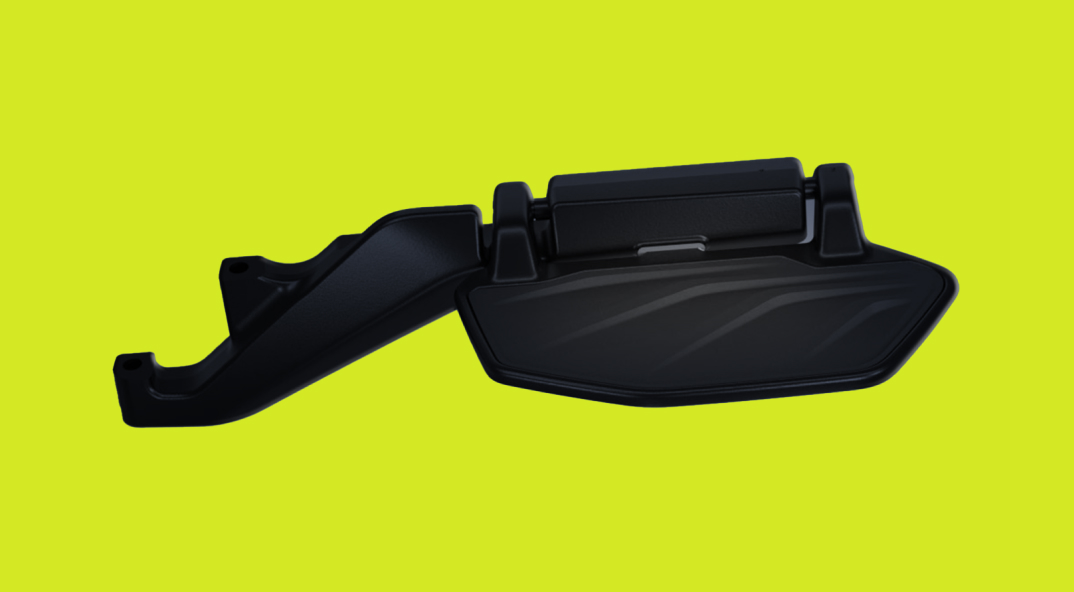
Managing multiple commodities in a project entails orchestrating sourcing players, establishing dedicated assembly lines, and accounting for quality, aesthetics, and demand fluctuations. This complexity involves numerous moving parts. We identified suitable partners for manufacturing this component, set targeted timelines, and ensured a streamlined Assembly Line managed by skilled operators. Mistake-proofing techniques were implemented to enhance efficiency and minimize errors. Quality standards, part qualification through AQL, and tool and part approval were defined. In addressing Delivery Planning, we managed raw material availability, assembly line logistics, Bill of Process (BOP), and downtime
Challenges
A Bengaluru-based electric two-wheeler manufacturer was all set to launch their new vehicle model in August 2022. Looking to develop a new side-step assembly for their vehicle in time for the launch, the company was looking for a partner who could handle a network of suppliers for the project, which involved multiple commodities, for end-to-end production, from raw material to delivery. This would require handling a robust supply chain to execute Tooling, DC, Spring, Machining, Plastic, BOP, Assembly, and Surface Finishing, manufacturing a volume of 6000 parts monthly, all within a three-month timeline.
Opportunities
Amidst these challenges, ZETWERK seized the opportunity to streamline the supply chain by leveraging its network of suppliers for end-to-end production. Advanced assembly line setup practices were implemented, incorporating best-in-class standards and efficiency measures. ZETWERK also capitalized on the opportunity to ensure quality assurance, define standards, implement AQL for part qualification, and secure quality tooling and approval. Efficient delivery planning became an opportunity to minimize gaps in the supply chain, mitigating risks and ensuring smooth inventory management.
Impact
ZETWERK completed the tooling and part approval process for the project within seven weeks. With dedicated teams for Quality Control, ZETWERK maintained best-in-class standards for parts qualifications and dimensions, with zero defects. AQL Sampling was set up to ascertain part qualification from an aesthetic point of view, with a black-anodized / matte surface finish. Poka-yoke practices ensured a smooth assembly line throughout the production cycle. Demand planning for raw materials, assembly line, BOP, and downtime ensured zero gaps, while smooth inventory management accounted for (+/-20%) variations in demand. ZETWERK cut down the lead time for development by four weeks, ensuring the project was delivered according to schedule.
Advantage
ZETWERK’s dedicated teams for project management and proprietary tools & technology-enabled seamless project management from the assembly line to the finish line. With a robust network of reliable suppliers, we were able to deliver the entire side-step assembly in August 2022, well in time for the new vehicle launch.
At ZETWERK, we turn challenges into precision opportunities, showcasing our commitment to excellence through streamlined supply chains and innovative quality practices